Energy Efficient Direct Drive Air Compressor Systems Milk Extra Work From Utility Dollars
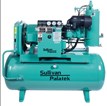
When it comes to wringing maximum utility out of every energy dollar, little things do mean a lot. In a report sponsored by the U.S. Dept. of Energy, the National Renewable Energy Laboratory concluded that, "Industrial electric motor systems account for more than 20% of all electricity used in the U.S.," and that, "using new technologies increases energy efficiency...improves profits." "By 2010," the report concludes, "using more efficient electric motor systems in the industrial sector could... provide an industrial energy cost savings of $13 billion." For these reasons and others, many commercial and industrial users of compressed air are turning to direct-drive electric air compressor systems.
As an example, if an efficient air compressor only requires 100 hp to supply a given air flow rate at a given pressure, vs. one with more moving parts that requires 112 hp, the savings in electrical costs can quickly yield a positive benefit/cost ratio on the more efficient machine. Using the industry standard average of $.08 cents per kWh, the 12 hp difference in this example would reduce electricity costs by approximately $4200 per year per unit.
"We use compressed air to disassemble motors and to remove motor parts, wheels and tires," says Jim Cook, Construction Manager of California-based Pick Your Part, the nation's leading self-service auto wrecker. "Now we use 25- and 30-HP direct drive units from Sullivan-Palatek to meet our demand for efficient air availability. The additional 30 HP we get from each new air compressor gives us added efficiency and economy," says Cook.
Sullivan-PalatekÒ of Michigan City, Indiana, manufacturers a line of direct-drive rotary-screw, industrial air compressor systems that allow users to profit from greater energy savings in their pressurized-air operations. The increased efficiency of this design stems from the use of larger air-end assemblies, which results in slower turning rotors that yield higher pressure using lower horsepower. Additional efficiency results from use of a direct-drive rotary screw that eliminates unnecessary moving parts such as belts, gears and pulleys—thus reducing the parasitic losses attributed to belts (4-8% loss) and gears (3-5%).
"We have an air compressor on four separate production lines to supply the cylinders that position woodworking tools," says Cory Bayer, maintenance team leader for Bayer Built Woodworks, Inc. of Belgrade, Minnesota, a major manufacturer of millwork. "We used regular piston compressors when our volume was less, but as we grew we needed more. So we switched over to the Sullivan-Palatek screw-type air compressors because they are more efficient and reliable enough to run the long hours that we needed."
Beyond energy efficiency, the challenge for any successful manufacturer is keeping up with demand so all industrial equipment must operate at maximum potential to capitalize fully on sales opportunities. For this reason, plant engineers and operations managers are looking to direct-drive electric air compressors to power their tools for longer durations with greater reliability.
"We used to use regular piston compressors when our volume was less, so it didn't matter that they could only run 60-70% of the time," recalls Bayer. "But as our business grew we needed an air compressor system that would run all the time, for up to 12 hours a day. So we switched over to the Sullivan-Palatek screw-type compressors because they are more heavy duty and reliable enough to run the long hours that we needed."
The increased reliability of Sullivan-Palatek's design stems from the use of larger air-end assemblies, which results in slower turning rotors that yield extended service life and higher pressure using lower horsepower. By eliminating moving parts such as belts, gears and pulleys, direct-drive rotary screw air compressors also have fewer moving parts; hence, they are less likely to fail or require service or replacement parts.
"I can't remember when we've ever had a Sullivan-Palatek unit break down," notes Bayer.
"We were frequently running out of air with our piston compressors," adds Cook of Pick Your Part. "But the direct-drive Sullivan-Palatek air compressors have held up to our constant demand for air with very little maintenance."
The most popular direct drive air compressors in the 5-60 HP range are manufactured by Sullivan-Palatek®. These small-but-mighty systems provide up to 8% improved efficiency and energy savings over gear- and belt-driven models, often resulting in saving thousands of kilowatt-hours of electricity per unit annually.
Cook says that although 25 HP Sullivan-Palatek compressors are standard with Pick Your Part, the firm installed a 30 HP model at its 64-acre Sun Valley, CA location. "We use such a high volume of air at that location that we now have installed a lead-lag (dual) system there. The additional 30 HP we get from the new unit gives us the necessary power margin."
As pneumatic actuators and direct-air blasts perform the bulk of processing duties in most plants, packers also find themselves turning to a new, direct-drive air compressor design to ensure maximum output and reliability.
"Up until about four years ago we had older, chain drive air compressors that kept breaking down and couldn't keep up with demand," says Tony Villalobos, operations manager for Sequoia Packing of Coalinga, California. "One broke down within a year's time, and when a compressor goes down I am out of business until the machine gets fixed. Since these models were too expensive to repair, I went out and bought a new Sullivan-Palatek unit. It had a great warranty, which impressed me. Once we used the first one, there was no doubt as to where the second air compressor was coming from. We got the other Sullivan-Palatek in 2003."
"We run these machines pretty hard, and they stand up to it," comments Villalobos. "There are no breakdowns. That's the important thing. In fact, right now I'm working on getting another one because we're getting so big that I need more."
SOURCE: Sullivan-Palatek